Genius RS-A is an entry-level cutting table that offers the same technological solutions to those used in automatic lines of the great industry. Genius RS-A is a solution that maintains over time a high cutting precision thus ensuring the return on investment and becoming one of the technological centres of the glass workshop. The idea behind the project is to put the glass companies in the world able to work with the same technological level of industrial groups ensuring a unprecedented level of reliability over time.

Ground worktable
The machine bed is made by a rigid frame onto which calibrated wooden panels are fitted in order to guarantee a high grade of flatness of the working area that is necessary to obtain the best results from the glass cutting or break-off operations.
Operating head
The operating head is equipped with an automatic cutting pressure control system. This mechanism controls the pressure of the cutting wheel from the very beginning to the end of the cut, automatically adjusting the pressure according to the geometry of the cutting path. The PC controlled axis speed and the high quality of all the electronic and mechanical components allow the optimisation of the cutting time, thus guaranteeing flexibility and continuity of operation.
Cut lubrication
The output of the oil used to lubricate the cutting wheel is regulated according to the cutting speed of the profile and the specific needs of the straight or shaped cuts, this eliminates waste improving at the same time the results of the machining. Accurate flow of the oiland prevention of the oil and drop effect
Optical reading of sheet orientation
The optical reader fitted to the operating unit recognises the position of the sheet on the worktable and allows to cut without the need to position the glass sheet against the stops, thus reducing waiting times and guaranteeing maximum precision in sheet positioning. This device also performs the function of a high precision dual zero when cutting laminated glass.
Precision mechanics
The mechanical processing on a machining centre of the frame in the parts where working plane is screwed and the rails and racks are positioned, the gantry axis cutting bridge, the use of recirculating ball guides combined with hardened and machined pinions and racks with helical teeth are usually characteristics that belong to machinery intended to cutting lines that work on two or three shifts and that process large volumes of glass. The result of all this technology on a single table offers the following performances:
- acceleration 10m / Sec.2
- speed 200 m / min.
- accuracy + – 0.15mm
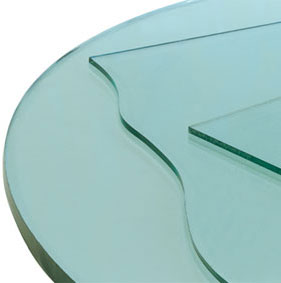

PC based numerical control IWNC (Intermac Windows Numerical Control)
The Genius RS-A also incorporates something completely new in the field of cutting tables: the IWNC numerical control integrated in a commercial personal computer operating a Windows interface. The use of a PC with Windows operating system is extremely simple and intuitive for the operator and provides full connectivity with commercially available network systems and optical/magnetic supports. The PC is supplied complete with DVD-ROM drive, modem and network card, 19” colour monitor and Windows operating system. The PC teleservice software enable remote diagnostics and software updating/modification through the use of a telephone line. It’s possible to connect a webcam to the PC, to save and transmit in real time instant images of some details of the machine to the Service Department.
Operator interface
The operator interface is simple to use and intuitive. It allows cutting programs generated by optimisers currently present on the market to be imported thanks to the presence of the OTD universal interface. The OTD (Optimizer Transferring Data) automatically defines the cutting parameters and generates the program for the Genius RS-A . The operator interface also allows rapid access to the cutting editor, to the parameter library, to the optimiser on board (opt.), to the new Icad program (opt.), even during the machine’s operating cycle, thus increasing productivity and reducing waiting times.
IEdit on board cut editor for straight and profile cuts
The cut editor for Windows, with its intuitive graphic interface, is used for making straight cuts on sheets without using the optimisation program. It is particularly useful for fast instantaneous cuts, it can manage countless levels and has a function for inserting profiles on the inside of sheets to be cut.
On board machine parameter library
Allows previously defined profiles to be adapted and the subsequent optimised cut directly on the machine control.
IOpty on board optimiser for straight and shaped cuts (opt.)
The Windows optimiser software with its detailed and intuitive graphic interface allows the cutting parameters to be defined automatically, speeding up set-up time and allowing straight and profile cuts to be optimised and subsequently stored as working programs. The software, which is used in particular for shaped and open cuts, allows even the most complex production to be optimised, guaranteeing minimum waste.
ICad system for shape creation (opt.)
A multitasking programming system operating under Windows for profile design with parameter programming and automatic geometric profile regeneration functions using the spline function. Allows automatic optimising and regenerating of artistic shapes in .dxf file format for the cutting of vinyl film.

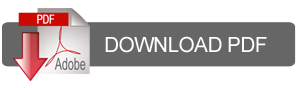